What is hot dip galvanizing
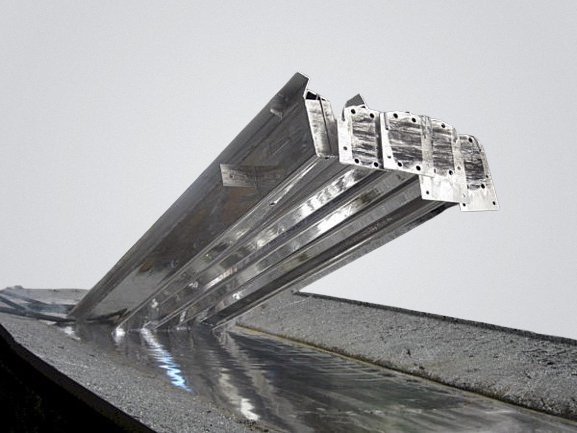
What are the benefits of hot dip galvanizing on products?
01
Introduction to hot dip galvanizing
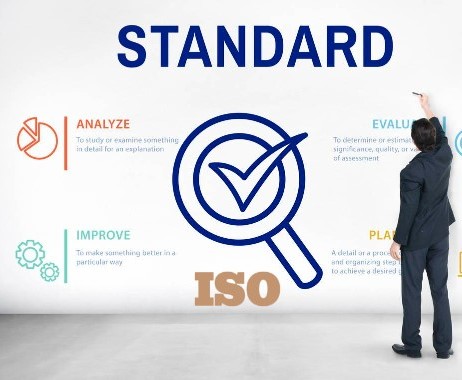
02
Domestic and foreign hot dip galvanizing specifications
Hot-dip galvanizing is a common anti-corrosion method that is often applied to metal surfaces, especially steel products, to protect them from corrosion.
These specifications typically cover various aspects of the hot-dip galvanizing process, including coating thickness, adhesion, surface condition, inspection methods, and test standards. For specific applications, the applicable specifications should be selected based on the local regulations and relevant industry standards.
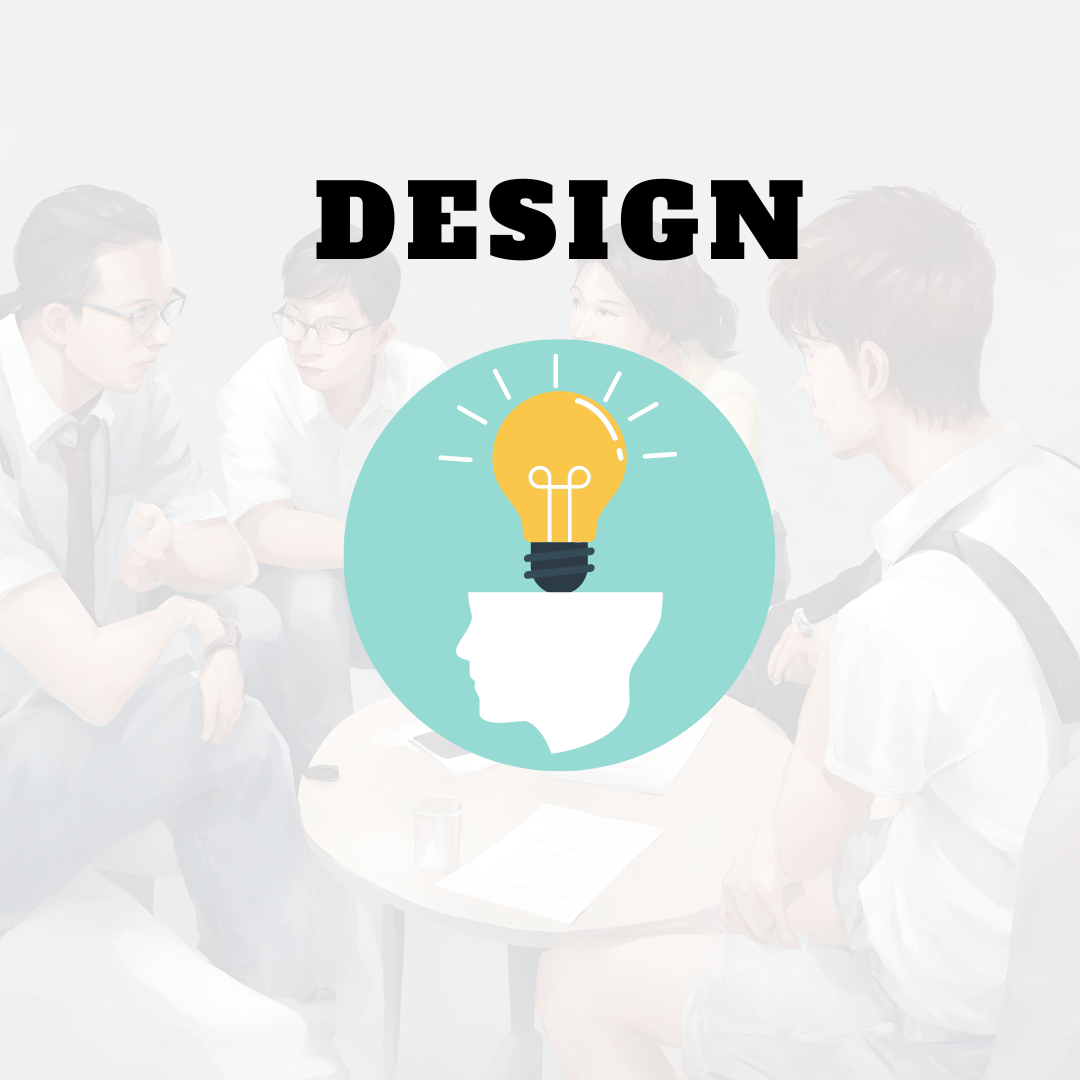
03
Design points
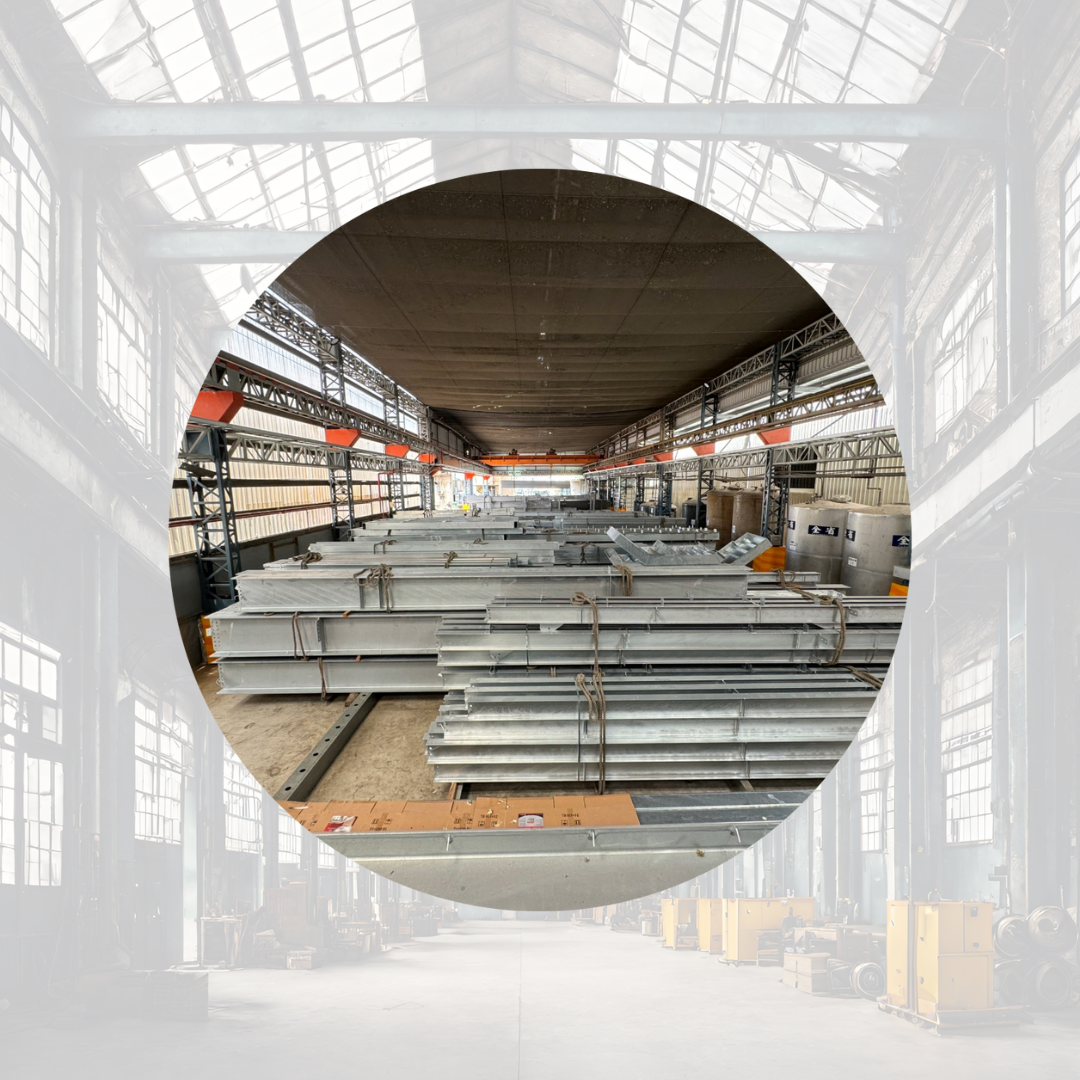
04
Hot dip galvanizing process
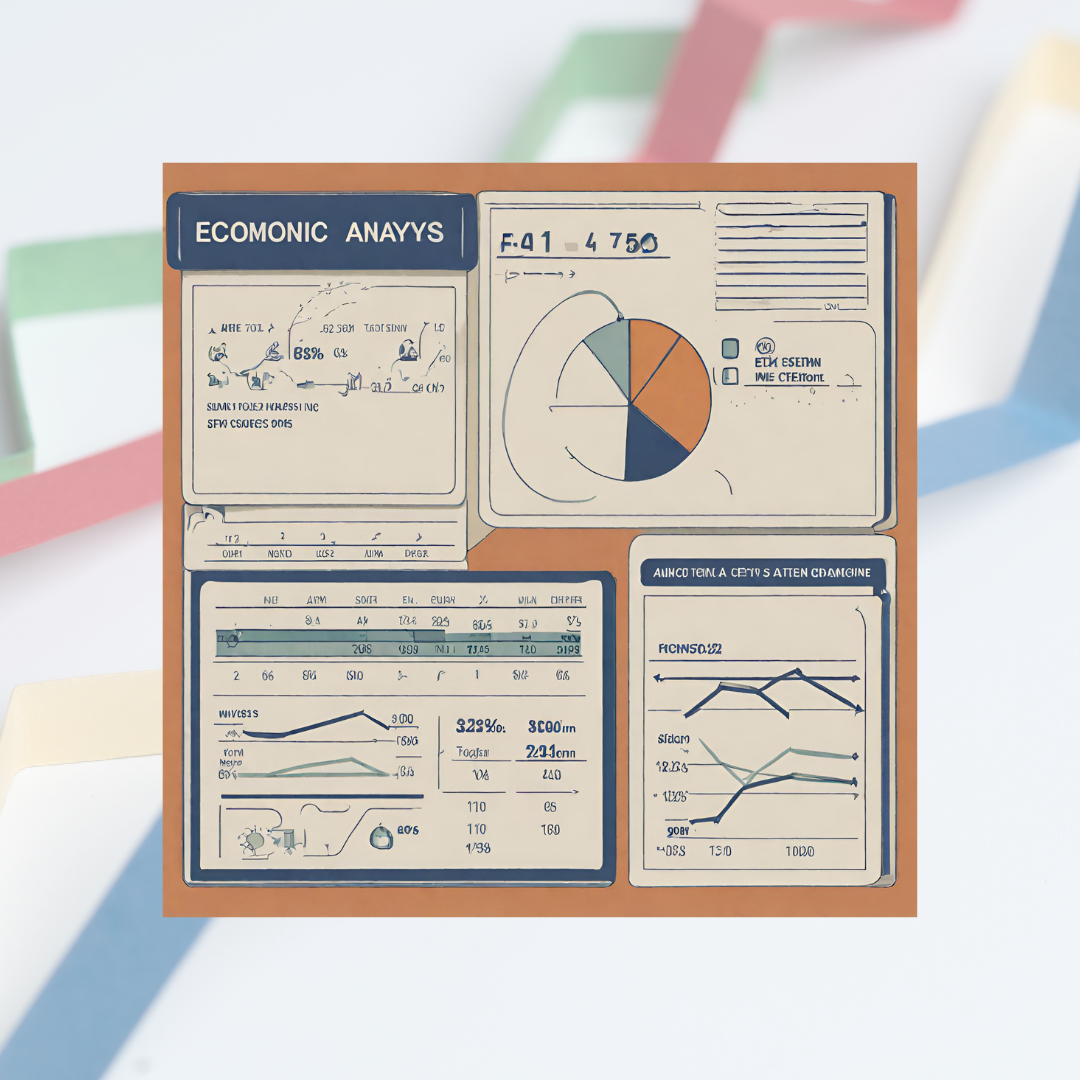
05
Economic Benefit Analysis
Considerations in selecting rust prevention systems are often based on economics. However, the initial cost often does not represent the overall cost required for various types of anti-rust systems.
Maintenance costs may vary significantly from system to system. If it is difficult to get close to the workpiece during maintenance, or the operation needs to be stopped, or additional products and machinery are required to cover the work, or scaffolding needs to be set up, etc., all of the above operations can significantly increase the cost of maintenance.
Since the size of the structure or work may affect the ease of treatment, it also affects the price of galvanizing. Unfortunately, it is not yet possible to establish the cost of galvanizing according to universal standards, but the same is true for other surface treatment systems.
Create a culture of hot dip galvanizing
Safeguard the world's limited resources
臺鍍科技股份有限公司
tg co., ltd.
20+
核心技術
35+
業界深耕
10000+
客戶肯定
臺鍍科技股份有限公司
tg co., ltd.
20+ core technologies
45+ years of entrepreneurship
10,000+customers affirmed
Create a culture of hot dip galvanizing
Safeguard the world's limited resources

Create a Hot-Dip galvanizing culture and safeguard the world’s limited resources
Head office
- 2nd Floor, No. 117, Section 1, Heping East Road, Daan District, Taipei City
- TEL / (02)2561-7665
- FAX / (02)2712-3686
- E-MAIL / info.tg@tgnet.com.tw
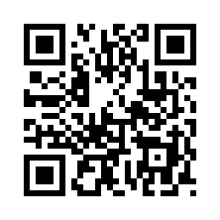
Hot-Dip galvanize
Product description
Latest news
Electronic publications
- 採用全球最先進SSL 256bit 傳輸加密機制
- 建議使用Chrome、Firefox、 Safari最新版本瀏覽