Introduction to hot dip galvanizing
Preface
01
Steel materials are indispensable and important resources in human life today. However, due to its own characteristics, "rust" accompanies us every day and consumes our resource - steel all the time. In particular, Taiwan is located in the harsh environment of the maritime monsoon with high temperature and humidity, and the "rust" problem is more serious than in other countries.
Advanced countries have noticed the seriousness of "corrosion" very early. It is estimated that the losses caused by corrosion prevention amount to approximately 3.5% of the gross national product (GNP) in Japan and 4.2% in the United States. %, 3.5% in the UK, 3% in Germany, and far more than the above countries in Taiwan. If calculated based on Japan's 3.5%, we unknowingly lost NT$586.565 billion in 2015 (the gross national product in 2015 was approximately NT$16.759 billion). Therefore, advanced countries have established relevant anti-corrosion technology research institutions to take various effective measures to avoid or reduce losses. However, there seems to be no major institution in our country to face up to this problem. Therefore, it is very sad to see “corroded” landscapes caused by poor anti-corrosion technology or wrong anti-corrosion methods everywhere.
Hot-dip galvanizing corrosion protection technology is currently the most widely used and most effective atmospheric corrosion protection method in advanced countries. Its performance, characteristics and economic benefits are all discussed in this introduction. We hope that through the explanation in this introduction, everyone will have a deeper understanding of the anti-corrosion method of hot-dip galvanizing and adopt it. I hope that we can soon see the calm and steady "zinc" color throughout Taiwan, filling every corner of our lives and shouldering the heavy responsibility of safeguarding our limited human resources.
Hot-dip galvanizing has been used for more than 170 years, and its principles remain unchanged. And because there are countless research reports on detailed reviews of its operation process, dry and continuous operations have evolved from the original wet galvanizing to the present. Its anti-corrosion effect is also recognized as the best and most economical at present. It is estimated that around 20,000,000 tons of steel are protected by hot-dip galvanizing every year around the world. Its value to the maintenance of limited human resources is really difficult to estimate.
Hot-dip galvanizing is widely used in advanced countries, including electricity, telecommunications, roads, transportation, bridges, harbors, buildings, etc. Therefore, it is not an exaggeration to say that "where there is iron, there is hot-dip galvanizing." Taiwan is located in a subtropical humid marine environment. Corrosion problems are more serious than those in other countries. However, due to insufficient vigilance on corrosion prevention issues, we can see steel abandoned due to corrosion everywhere. It is really worth mentioning. People think deeply.
Advantages of hot dip galvanizing
02
- The entire iron surface is protected. No matter inside the recessed pipe fitting or any other corner where the coating is difficult to enter, the molten zinc can be easily and evenly covered.
- The entire iron surface is protected. No matter inside the recessed pipe fitting or any other corner where the coating is difficult to enter, the molten zinc can be easily and evenly covered.
Base steel is the original iron base, with a general hardness of about 159 DPN hardness.
Zeta layer is the dense alloy layer closest to the iron base. It has a complex structure, is rich in toughness and ductility, and exists as Fe Zn7. The iron content is about 7~11%.
The δ1 layer (Delta layer) is a significant monoclinic columnar structure, formed from Fe Zn13, with an iron content of about 6% and a hardness value of about 179 DPN.
The pure zinc layer at the top of the eta layer is a dense hexagonal crystal system. It is soft and ductile and is not easy to break during deformation processing. The purity of zinc is about 98.5% or more, and the hardness value is about 70 DPN.
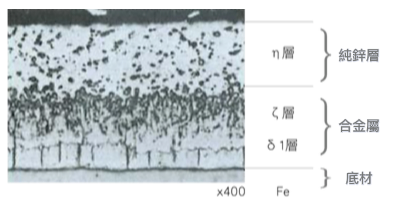
圖 1:熱浸鍍鋅皮膜斷面顯微鏡組織
- In the corner areas, the zinc layer is often thicker than in other places (as shown in Figure 2), and has good toughness and wear resistance. The corners of other coatings are often the thinnest, most difficult to apply, and most vulnerable to damage, so they often need to be maintained.
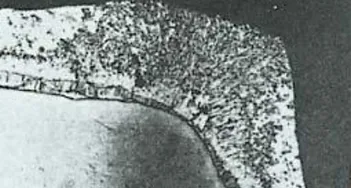
Figure 2: The galvanized layer on the corners of steel components is thicker
- Even if a small part of the zinc layer falls off due to heavy mechanical damage or other reasons, leaving the steel substrate exposed, the zinc layer around this area will function as a sacrificial anode to protect the steel from damage. Erosion. On the other hand, other anti-corrosion methods are just the opposite. Rust will form immediately and quickly spread to the bottom of the coating, causing the coating to peel off (as shown in Figure 3).
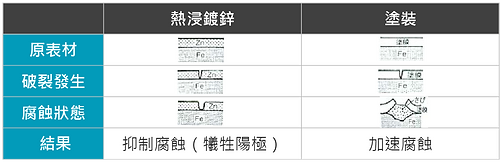
Figure 3: Corrosion difference between galvanized layer and paint cracks
- The consumption of zinc layer in the atmosphere is very slow, as shown in Figure 4, which is about 1/17 to 1/18 of the steel corrosion rate, and is predictable. Its service life is far longer than other anti-corrosion methods.
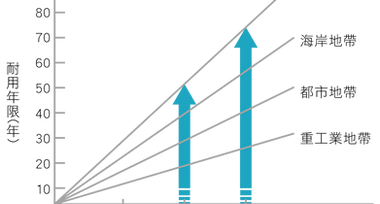
Figure 4: Durability life of hot-dip galvanizing
- The service life of the galvanized layer in a certain environment mainly depends on the thickness of the galvanized layer. The thickness of the coating is also affected by the thickness of the steel. That is, the thicker the steel, the easier it is to get a thicker coating. Therefore, the thicker steel parts in the same steel structure will definitely get a thicker coating and a longer life. ( As shown in Figure 5).
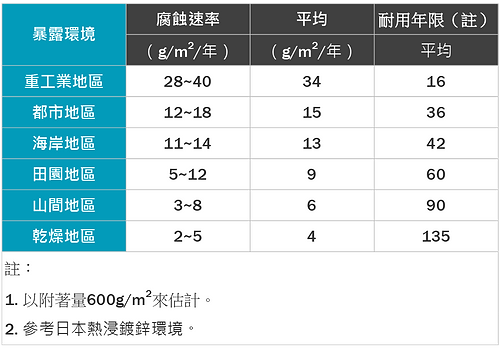
Figure 5: Corrosion rates of hot-dip galvanizing in various environments
- Due to aesthetics, art, or extremely corrosive environments, a duplex system of paint can be applied to the galvanized layer. As long as the paint system is correctly selected and the construction is easy, the anti-corrosion effect will last longer than paint alone or hot-dip galvanizing. The added value is even better, approximately 1.5 to 2.5 times the lifespan. (Figure 6)
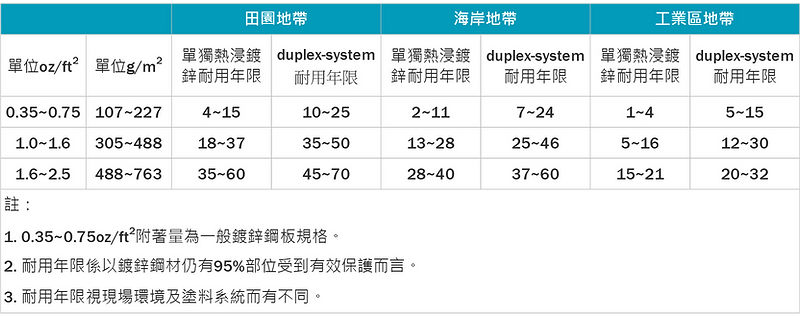
Figure 6: Comparison of service life between hot-dip galvanizing and hot-dip galvanizing plus paint (duplex-system)
- In addition to hot-dip galvanizing, there are other methods to protect steel with zinc layers. Comparing their advantages and disadvantages (as shown in Figure 7), the method that is generally the most widely used, has the best anti-corrosion effect and has the best economic benefits is hot-dip galvanizing. Dip galvanizing method.
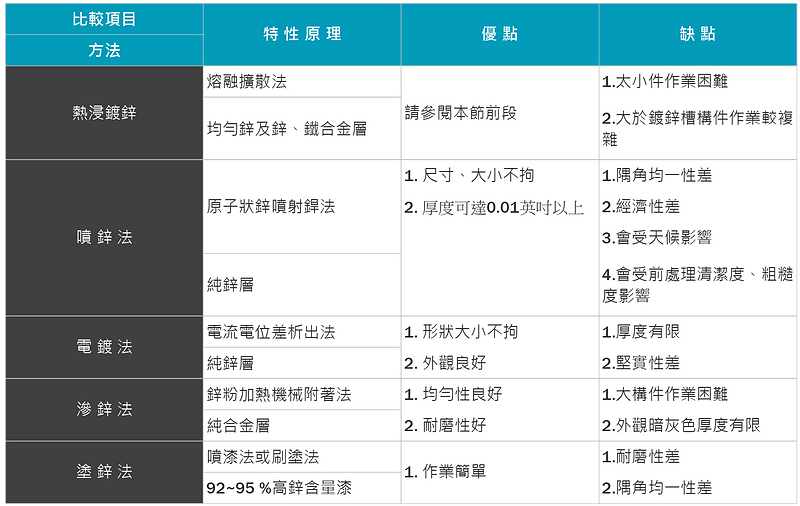