Hot dip galvanizing process
Process introduction
01
The principle of hot-dip galvanizing is simply to immerse the cleaned iron parts into a zinc bath through the wetting effect of Flux, so that the steel and molten zinc react to form an alloyed film.
A good hot-dip galvanizing operation should ensure that each process is under strict control and that the functions of the process can be fully utilized. Moreover, if the previous process is defective, it will cause a chain reaction of adverse reactions in the subsequent processes, which will greatly increase the operating cost or result in defective hot-dip galvanizing products. If the pretreatment is poor, the molten zinc cannot fully react with the steel to form a perfect galvanized layer structure. If the post-processing is poor, the appearance of the galvanized layer will be easily damaged and the commercial value of the galvanized layer will be reduced.
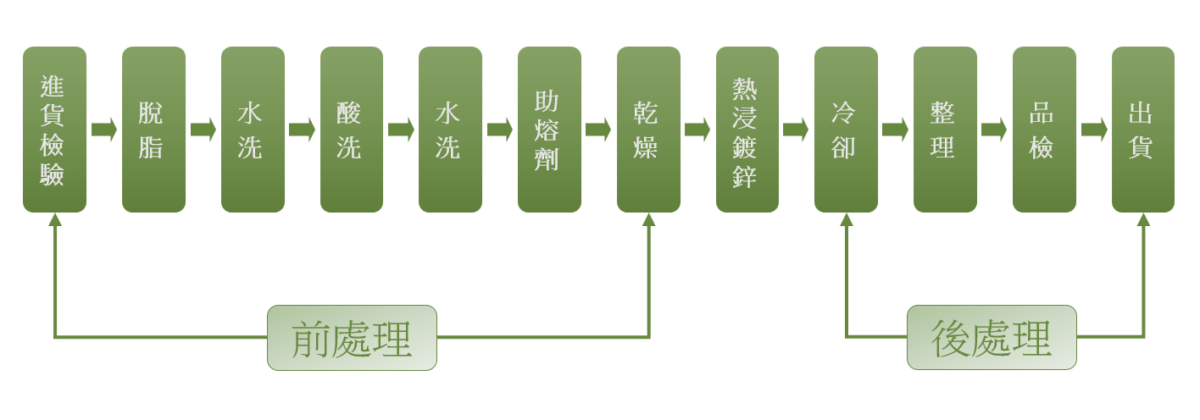
The process is detailed below
Process introduction
02
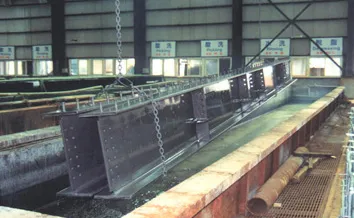
Degreasing
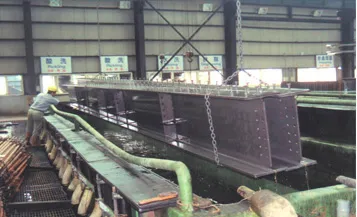
Pickling
使用硫酸去除被鍍件的表面鐵鏽。
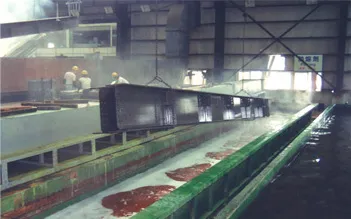
Fluxing
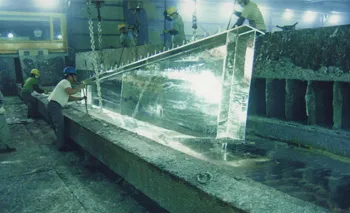
Galvanizing
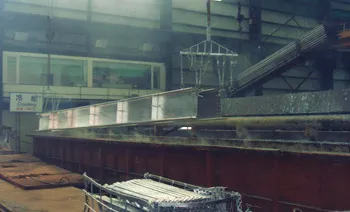
Cooling
